A Comprehensive Guide to Shock Freezer Rooms and Devices
6 July 2024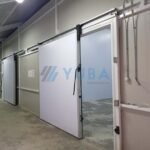
The Future of Industrial Cooling Systems in Europe: Cutting-Edge Solutions for Your Business
15 July 2024Understanding Industrial Cooling Systems
Industrial cooling systems are pivotal in maintaining optimal temperature and climate control across a wide range of industries. These systems encompass various technologies, including HVAC systems, refrigeration units, and industrial chillers, each designed to meet specific cooling needs. HVAC systems, or heating, ventilation, and air conditioning systems, are commonly used for maintaining ambient conditions in industrial facilities. They ensure that the indoor environment remains conducive for both workers and sensitive equipment.
Refrigeration units play a crucial role in industries such as food processing and pharmaceuticals, where precise temperature control is essential for product quality and safety. These units use refrigerants to absorb and dissipate heat, keeping products at the desired temperature. Industrial chillers, on the other hand, are often employed in manufacturing processes to remove heat generated by machinery and processes, thereby preventing overheating and maintaining efficiency.
The importance of these cooling systems extends to the concept of cold storage and the cold chain. Cold storage facilities are specialized environments where perishable goods, such as food and pharmaceuticals, are stored at controlled temperatures to extend their shelf life and maintain their quality. The cold chain refers to the continuous sequence of refrigerated production, storage, and distribution activities, along with associated equipment and logistics. This chain is vital for ensuring that perishable products remain safe and effective from the point of origin to the final consumer.
In essence, these industrial cooling solutions are indispensable for various sectors. In manufacturing, they mitigate the risk of equipment failure due to overheating. In the food processing industry, they prevent spoilage and contamination. In pharmaceuticals, they ensure the efficacy of temperature-sensitive medications. By maintaining stringent temperature control and climate conditions, industrial cooling systems safeguard product integrity, enhance operational efficiency, and contribute to overall safety and quality.
Energy Efficiency and Sustainable Cooling Solutions
Energy efficiency is a critical consideration in the realm of industrial cooling, where significant energy consumption can lead to high operational costs and considerable environmental impact. By optimizing energy use, companies can not only reduce expenses but also contribute to environmental sustainability. Innovative technologies and practices, such as advanced refrigerants, variable speed drives, and smart controls, play a pivotal role in enhancing the efficiency of cooling systems.
Advanced refrigerants, for instance, are designed to deliver superior cooling performance while minimizing energy usage and reducing the environmental impact. These refrigerants often have lower Global Warming Potential (GWP) compared to traditional options, helping to decrease the carbon footprint of industrial refrigeration units. Additionally, the implementation of variable speed drives in cooling equipment allows for better control over motor speed, leading to significant energy savings by adjusting the cooling output to match the exact requirements of the process.
Smart controls are another crucial innovation in industrial cooling technology. By utilizing intelligent algorithms and real-time data analysis, these systems can optimize the operation of cooling systems, ensuring they run at peak efficiency. This not only reduces energy consumption but also enhances the overall performance and reliability of refrigeration units.
Sustainable cooling solutions are also gaining traction, with a focus on eco-friendly refrigerants and renewable energy sources. For example, natural refrigerants such as ammonia and carbon dioxide are increasingly being adopted due to their negligible environmental impact. Furthermore, integrating renewable energy sources like solar or wind power into cooling systems can significantly reduce dependency on fossil fuels, further lowering the carbon footprint.
Several companies have successfully implemented these innovative and sustainable cooling solutions. One notable example is a leading food processing company that replaced its conventional refrigeration systems with advanced, energy-efficient chillers using natural refrigerants. This transition resulted in a 30% reduction in energy consumption and a substantial decrease in greenhouse gas emissions. Another case study involves a pharmaceutical firm that integrated solar power with its cold storage facilities, achieving both energy savings and enhanced sustainability.
These examples highlight the tangible benefits of embracing energy-efficient and sustainable cooling solutions in industrial applications. As technology continues to evolve, the future of industrial cooling promises even greater advancements in efficiency and environmental stewardship.
Maintenance and Management of Cooling Systems
Effective maintenance and management are crucial for ensuring the optimal performance and longevity of industrial cooling systems. Regular maintenance tasks, such as cleaning coils and checking refrigerant levels, are foundational to sustaining energy efficiency and preventing unexpected system failures. Clean coils enhance heat transfer efficiency, reducing the workload on refrigeration units and thereby lowering energy consumption. Likewise, maintaining proper refrigerant levels ensures that cooling systems operate within their designed parameters, preventing undue stress on components and optimizing cooling performance.
More complex procedures involve the periodic inspection and replacement of critical components. For instance, inspecting compressors, fans, and evaporators for wear and tear can preempt catastrophic failures. Replacing worn-out parts before they fail not only extends the life of the cooling equipment but also minimizes downtime and repair costs. Advanced diagnostic tools play a vital role in this aspect, allowing for precise monitoring of system performance and early detection of issues. Tools such as infrared thermography and vibration analysis can identify anomalies that are not visible to the naked eye, enabling proactive maintenance strategies.
Regular system audits and continuous monitoring are also essential practices. Conducting comprehensive audits helps identify inefficiencies and potential problems, providing an opportunity to make necessary adjustments or upgrades. Monitoring systems in real-time allows for immediate response to any irregularities, maintaining consistent temperature control and ensuring the integrity of cold storage and cold chain operations. This is particularly important in industries where precise climate control is critical, such as food processing, pharmaceuticals, and chemical manufacturing.
The role of trained personnel cannot be overstated. Skilled technicians equipped with the latest knowledge and tools are indispensable for maintaining industrial chillers and other cooling installations. Ongoing training programs ensure that staff remain proficient in the latest cooling technologies and maintenance techniques, fostering an environment of continuous improvement and operational excellence.
Overall, a combination of routine maintenance, advanced diagnostics, regular audits, and skilled personnel forms the backbone of effective cooling system management. This holistic approach not only enhances the reliability and efficiency of industrial cooling solutions but also contributes to energy efficiency and sustainability goals, supporting eco-friendly cooling practices in the long run.
Future Trends in Industrial Cooling Technology
The landscape of industrial cooling is poised for significant transformation, driven by advances in technology and an increasing emphasis on sustainability. One of the key trends shaping the future is the development of more compact and efficient refrigeration units. Modern designs are focusing on reducing the footprint of cooling equipment while enhancing their performance and energy efficiency. This is particularly crucial for industries with limited space but high cooling demands.
Digitalization and the Internet of Things (IoT) are revolutionizing the way cooling systems operate. Smart sensors and data analytics are being integrated into refrigeration units to enable real-time monitoring and predictive maintenance. This allows for precise temperature control and early detection of potential issues, significantly reducing downtime and maintenance costs. By leveraging IoT, companies can achieve superior climate control and ensure the reliability of their cold storage and industrial chillers.
Sustainability is becoming a cornerstone of industrial cooling solutions. Regulatory changes are pushing for the adoption of eco-friendly cooling technologies that minimize environmental impact. Innovations such as natural refrigerants and energy-efficient cooling systems are gaining traction. These sustainable cooling technologies not only comply with stricter regulations but also contribute to overall energy savings and reduced carbon footprints.
Looking ahead, the integration of artificial intelligence (AI) and machine learning into cooling system management holds great promise. AI can optimize the performance of HVAC systems by learning usage patterns and adjusting operations for maximum efficiency. This can lead to significant energy savings and improved operational efficiency over time. Machine learning algorithms can also enhance predictive maintenance by accurately forecasting equipment failures and suggesting timely interventions.
In conclusion, the future of industrial cooling technology is being shaped by advancements in equipment design, digitalization, and a growing focus on sustainability. As industries continue to adopt smarter and greener cooling solutions, we can expect improved efficiency, reduced environmental impact, and more reliable temperature control across various applications.